Mirror Worlds Explained: The Power of Digital Twins in Industry and Design
Explore the concepts of Mirror Worlds and Digital Twins. Learn how these dynamic virtual replicas, linked to real-world counterparts through data, are transforming manufacturing, urban planning, healthcare, product design, and more. Understand the underlying technologies, key benefits, implementation challenges, ethical considerations, and the future trajectory of this powerful innovation.
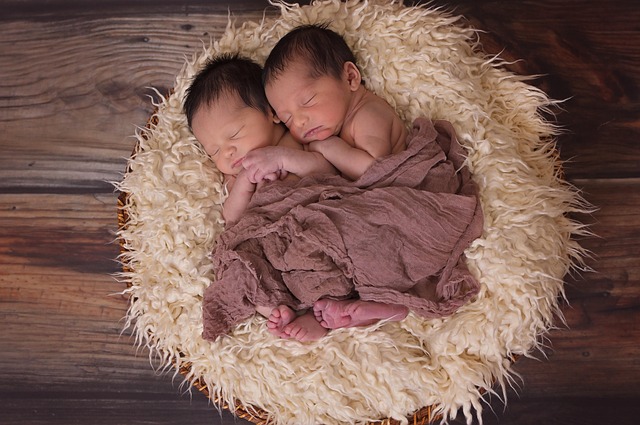
1. What Are Mirror Worlds and Digital Twins?
Learning Objectives: * Define Mirror Worlds and Digital Twins, understanding their relationship. * Trace the key technological advancements that enabled Digital Twins. * Clearly differentiate Digital Twins from static simulations based on their dynamic data connection. * Grasp the core value proposition: bridging the physical and digital realms for enhanced insight and interaction.
Introduction: Imagine a world where every significant physical object, system, or even environment has a living, evolving digital counterpart - a dynamic mirror accessible through technology. This grand, overarching vision is often called a 'Mirror World'. Within this vision, the practical building blocks are Digital Twins: powerful, dynamic virtual replicas that are revolutionizing how we design, operate, monitor, and interact with the physical world.
Defining Mirror Worlds: The term 'Mirror Worlds', popularized by Yale computer scientist David Gelernter in his 1991 book, envisions a comprehensive, real-time, digital representation of the entirety of physical reality. Think of it not just as a static map, but as a dynamic, interactive, 1:1 scale digital layer overlaid on the world, constantly updated with data flowing from real-world activities. This could encompass geography, city operations, factory floors, global supply chains, and potentially even biological systems. While a complete Mirror World remains largely conceptual due to its immense scale and complexity, the technologies enabling its constituent parts - Digital Twins - are rapidly maturing.
Defining Digital Twins: A Digital Twin is a more focused and practical concept. It's a dynamic virtual model of a specific physical asset (like a wind turbine), process (like an assembly line), or system (like a city's traffic network or a patient's heart). What truly distinguishes a Digital Twin from a mere blueprint or simulation is its continuous, dynamic connection to its physical counterpart. It's constantly updated with real-time or near real-time data gathered by sensors (part of the Internet of Things - IoT) and other connected data sources. This data stream allows the Digital Twin to accurately mirror the actual state, condition, performance, and behavior of the physical entity throughout its entire lifecycle. It's not just a static snapshot; it's a living digital counterpart.
Historical Context and Evolution: The core idea of modeling reality isn't new. Engineers have used Computer-Aided Design (CAD) for decades to create detailed digital blueprints, and simulation software to test designs virtually. However, these were typically static representations used before physical creation or for offline analysis, fundamentally disconnected from the operating asset. The transition to dynamic Digital Twins was sparked by the convergence of several key technologies, particularly over the last two decades: 1. IoT (Internet of Things): Affordable, capable sensors collecting vast amounts of real-time operational and environmental data directly from physical objects. 2. Connectivity: Reliable, fast networks (like 5G, Wi-Fi 6, LPWAN) capable of transmitting this data deluge efficiently from sensors to processing platforms. 3. Cloud Computing: Scalable, accessible platforms providing the necessary storage capacity and computational power to manage and process massive data streams. 4. AI/ML (Artificial Intelligence / Machine Learning): Advanced algorithms needed to analyze the complex data, identify subtle patterns, predict future states (like potential failures or performance bottlenecks), and recommend optimizations.
This technological convergence transformed static models into living, data-driven Digital Twins that evolve alongside their physical counterparts, enabling continuous monitoring, sophisticated analysis, and powerful predictions.
Distinguishing from Static Simulations: The critical differentiator is the dynamic, often bidirectional, data link. A static simulation might model how a bridge should theoretically behave under a specific load based on design parameters. A Digital Twin of that bridge, however, continuously ingests real-time data from sensors measuring actual stress, vibration, temperature, and traffic flow, reflecting its current, real-world condition. It can then run simulations based on this live context to predict potential issues (like fatigue damage under current conditions) or optimize maintenance. Data flows from the physical asset to the digital model, enriching it with real-world context. Crucially, insights or commands derived from the model can then flow back to inform actions (manual or automated) on the physical asset (e.g., adjusting operational parameters, scheduling maintenance). The Digital Twin isn't just a passive model; it's an interactive, data-connected counterpart.
The Core Value: The fundamental value of Digital Twins (and the broader Mirror World concept) lies in bridging the gap between the physical and digital worlds. This persistent, dynamic connection unlocks significant advantages: * Deep Understanding: Gaining unprecedented insights into the real-time performance, condition, and behavior of physical assets and processes, moving beyond assumptions or historical averages. * Prediction: Forecasting future behavior, potential failures, resource needs, or operational outcomes based on current and historical data, enabling proactive management. * Optimization: Testing the impact of changes (e.g., process adjustments, design modifications, different operating scenarios) virtually within the Digital Twin before implementing them physically, thereby reducing risks, costs, and time. * Interaction & Control: Enabling remote monitoring, diagnostics, and, in some cases, direct control or automated adjustments of physical systems based on analysis and commands originating from the Digital Twin.
Analogy: Blueprint vs. Smart Home System Think of a static architectural blueprint versus a modern smart home system: * The blueprint shows the house's design (like a CAD model or static simulation) - its structure and intended layout. * The smart home system is more like a Digital Twin: * It shows the current status: temperature, which lights are on, security sensor readings (Real-time Data). * It can analyze patterns and predict future energy usage based on current settings and historical data (Prediction). * It allows you to virtually test dimming lights or changing thermostat schedules to see the potential impact on comfort or cost (Optimization through Simulation). * It lets you remotely adjust the thermostat, lock doors, or turn off lights (Interaction & Control). A Digital Twin provides this kind of dynamic insight, prediction, optimization, and control for complex industrial assets, processes, and systems.
Key Concepts: * Mirror World: A comprehensive, real-time, interconnected digital representation of the physical world (largely a conceptual vision). * Digital Twin: A dynamic virtual representation of a specific physical asset, process, or system, linked by real-time data throughout its lifecycle. * IoT (Internet of Things): A network of physical objects embedded with sensors, software, and connectivity enabling them to collect and exchange data. * Real-time Data: Information collected and transmitted almost instantaneously, reflecting the current state of the physical counterpart. * Bidirectional Link: Data flows from physical to digital for monitoring and analysis, and insights/commands can flow from digital back to physical, enabling interaction and control.
Knowledge Check: 1. What is the primary difference between a Digital Twin and a traditional CAD model or static simulation? * a) Digital Twins use 3D graphics, while CAD models don't. * b) Digital Twins are dynamically linked to their physical counterparts via real-time data streams, reflecting their current state and enabling interaction. * c) Digital Twins are only used for manufacturing. * d) CAD models are inherently more accurate than Digital Twins. (Correct Answer: b)
Summary: Mirror Worlds represent the ambitious vision of digitally replicating reality, while Digital Twins are the practical, focused implementations for specific assets or processes. Evolved from static models, Digital Twins leverage the convergence of IoT, connectivity, cloud computing, and AI/ML to create dynamic, data-driven virtual counterparts. They are defined by their continuous, often bidirectional, data link to the physical world. Their core value lies in bridging the physical and digital realms, enabling deeper understanding, accurate prediction, risk-free optimization, and enhanced interaction, fundamentally changing how we manage complex systems.
2. The Technology Stack: Building a Digital Twin
Learning Objectives: * Identify the key technological layers required to build and operate a Digital Twin. * Understand the function of IoT sensors and edge devices in acquiring data from the physical world. * Recognize the importance of various connectivity options and their security implications. * Appreciate the roles of cloud and edge platforms in processing and storing vast amounts of data. * Understand the critical need for data integration, contextualization, and robust management. * Grasp how AI/ML and visualization tools transform data into actionable insights.
Introduction: Creating a functional Digital Twin isn't about deploying a single piece of software. It requires orchestrating a complex ecosystem of interconnected technologies - often referred to as the 'technology stack'. This stack works in concert: sensing the physical world, securely transmitting data, processing it into information, deriving insights through analysis, and presenting those insights effectively for decision-making. Understanding these layers is crucial for implementing and leveraging Digital Twins successfully.
1. Sensing Layer: IoT Sensors and Edge Devices: This is where the physical world meets the digital realm. Sensors are embedded within or attached to the physical asset to capture raw data about its state, operation, and environment. * Types of Sensors: Temperature, pressure, vibration, GPS location, optical (cameras), acoustic, chemical composition, strain gauges, lidar, radar, flow meters, energy meters, etc. The choice depends entirely on what aspects of the physical asset need monitoring to achieve the specific goals of the Digital Twin (e.g., predicting failure, optimizing energy). * Edge Devices & Edge Computing: Raw sensor data is often pre-processed locally on 'edge devices' (like smart gateways, Programmable Logic Controllers (PLCs), or dedicated edge computers) situated near the data source. Why process at the edge? Edge computing can: * Reduce Latency: Perform initial analysis and trigger time-sensitive actions faster than sending data to a distant cloud. * Minimize Bandwidth: Filter noise, aggregate data, or perform compression to reduce the volume of data transmitted over the network, saving costs. * Enhance Resilience: Allow some functionality even if cloud connectivity is temporarily lost. * Improve Security: Perform initial data encryption and anomaly detection locally.
2. Connectivity Layer: Data Transmission: Once collected (and potentially pre-processed), data must be reliably and securely transmitted to where it can be further processed and stored (often the cloud, but sometimes other edge locations or on-premise servers). * Key Considerations: Bandwidth (how much data?), latency (how fast?), reliability (will it get there?), security (is it protected?), power consumption (especially for battery-powered sensors), and range (distance) are critical factors in choosing the right technology. * Technologies (Trade-offs): Choices vary widely: * 5G/Cellular: High bandwidth, low latency, wide area mobility (good for mobile assets, large factories, smart cities). * Wi-Fi (e.g., Wi-Fi 6/6E): Good bandwidth, lower cost than cellular, suitable for dense indoor environments (factories, buildings). * LPWAN (LoRaWAN, NB-IoT, Sigfox): Low power, long-range, but low bandwidth (ideal for sensors sending infrequent small data packets like environmental readings or simple status updates). * Wired Ethernet: High reliability, speed, and security (best for fixed assets where cabling is feasible). * Satellite: Coverage for very remote assets lacking terrestrial network access. * Security: This layer is a critical point for security. Robust protocols for secure data transmission (e.g., TLS/SSL encryption) and strong device authentication are essential to prevent unauthorized access, data interception, or tampering.
3. Data Processing and Storage Layer: Cloud and/or Edge Platforms: This is the 'brain' where raw data is aggregated, stored, processed, and transformed into meaningful information. This often involves both cloud and edge resources working together. * Cloud Platforms (e.g., AWS IoT, Azure Digital Twins, Google Cloud IoT): Offer virtually unlimited scalability for storage (using data lakes for raw data, time-series databases optimized for timestamped sensor readings, etc.), powerful computing resources for complex AI/ML model training and execution, and managed services for IoT device management, data ingestion, security, and visualization. * Edge Computing: As noted, processing can occur closer to the data source for immediate needs. Often, a hybrid approach is optimal, using the edge for real-time tasks and the cloud for large-scale analysis, model training, and long-term storage. * Data Handling: Platforms must handle diverse data types: structured (sensor readings in tables), semi-structured (JSON logs), and unstructured (images, video feeds, maintenance text reports).
4. Data Integration and Management: This is often the most challenging layer. Data arrives from diverse sources (sensors, enterprise systems like ERP/MES/PLM, design files, external sources like weather forecasts) in different formats, frequencies, and levels of quality. * Integration: Combining data from these various silos to create a unified, holistic view. This requires APIs (Application Programming Interfaces), standard data formats, messaging protocols (like MQTT, AMQP), and industrial protocols (like OPC-UA) to enable systems to talk to each other. * Contextualization: This is crucial. It involves adding meaning and relationships to raw data points. For example, linking a specific temperature reading not just to a timestamp, but to the machine it came from, the component within that machine, its operational phase at the time, and its recent maintenance history. Without context, data is just numbers. * Data Governance: Implementing policies and procedures to ensure data quality (accuracy, completeness, timeliness), security, access control, lineage tracking (where did data come from?), and compliance with regulations. * Modeling/Semantics: Defining the structure, properties, and relationships within the digital twin (e.g., using standardized ontologies or definition languages like Azure's Digital Twin Definition Language - DTDL) so that data can be understood consistently.
5. Analysis Layer: AI and Machine Learning: This layer unlocks the predictive and prescriptive power of the Digital Twin by applying algorithms to the integrated, contextualized data. * Types of Analytics: * Descriptive: What is happening now? (Real-time monitoring, dashboards, alerts). * Diagnostic: Why did it happen? (Root cause analysis, identifying factors contributing to events). * Predictive: What is likely to happen next? (Predicting failures, forecasting demand, simulating future performance). * Prescriptive: What should we do about it? (Recommending optimal maintenance, suggesting process adjustments, automating responses). * Algorithms: AI/ML techniques are key enablers. Common methods include time-series analysis, regression, classification, clustering, anomaly detection, natural language processing (for text data), computer vision (for images/video), physics-based modeling (combining data with engineering principles), and reinforcement learning (for autonomous optimization).
6. Visualization and Interaction Layer: This is how humans interact with the Digital Twin, consume its insights, and ultimately derive value. * Dashboards: Displaying Key Performance Indicators (KPIs), real-time status, historical trends, and alerts in an easily digestible format. * 3D Models: Providing an intuitive visual representation of the physical asset, often overlaid with real-time data (e.g., color-coding components by temperature or stress) or simulation results. * Simulation Tools: Allowing users to run 'what-if' scenarios (e.g., "What happens if I increase this machine's speed?") and visualize the potential outcomes. * AR/VR/MR (Extended Reality - XR) Interfaces: Creating immersive experiences where users can interact with the Digital Twin overlaid on the physical world (Augmented/Mixed Reality) or within a fully virtual environment (Virtual Reality) for tasks like complex maintenance guidance, remote expert assistance, design reviews, or virtual training. * APIs: Enabling other applications or automated systems to programmatically access Digital Twin data and functionality.
Visualization Example: Imagine using a tablet with AR: pointing it at a complex pump system reveals a 3D overlay. Tapping on a specific bearing displays its real-time vibration signature, temperature trend, a stress analysis visualization derived from current operating conditions, and its predicted remaining useful life based on an AI model - all updated dynamically.
Key Concepts: * Technology Stack: The layered ecosystem of hardware and software technologies enabling a Digital Twin, from sensors to visualization. * Edge Computing: Processing data closer to its source for benefits like speed, efficiency, and resilience. * Data Integration: Combining and harmonizing data from disparate sources into a unified view. * Data Contextualization: Adding meaning and relationships to raw data points to make them interpretable. * Predictive Analytics: Using historical and real-time data with statistical and machine learning models to forecast future events or states. * Visualization: Presenting complex Digital Twin data and insights in an understandable and actionable format (dashboards, 3D models, AR/VR).
Knowledge Check: 1. Why might edge computing be preferred over sending all raw sensor data directly to the cloud for a time-sensitive industrial control application? * a) Edge devices have more storage capacity than the cloud. * b) Cloud computing is inherently less secure than edge computing. * c) To reduce latency for faster analysis and response times, filter noisy data locally, minimize network bandwidth usage and cost, and maintain some function during network outages. * d) Edge computing requires less sophisticated sensors. (Correct Answer: c)
Summary: Building a Digital Twin involves integrating multiple technological layers, forming a comprehensive stack. It starts with IoT sensors and edge devices capturing data from the physical world. This data is securely transmitted via suitable connectivity networks to cloud and/or edge platforms for storage and processing. Robust data integration, contextualization, and management are crucial to handle diverse data sources and add meaning. AI and Machine Learning algorithms then analyze this prepared data to provide descriptive, diagnostic, predictive, and prescriptive insights. Finally, visualization tools - including dashboards, 3D models, and XR interfaces - allow users to interact with, understand, and act upon the Digital Twin's information, completing the cycle from physical asset to actionable digital insight.
3. Revolutionizing Industry: Manufacturing and Operations
Learning Objectives: * Identify key applications and benefits of Digital Twins in manufacturing and industrial operations (Industry 4.0). * Understand how Digital Twins enable Predictive Maintenance (PdM) and its advantages over traditional maintenance approaches. * Recognize the value of using Digital Twins for process simulation, virtual commissioning, and operational optimization. * Appreciate the role of Digital Twins in enhancing supply chain visibility, resilience, and quality control. * Understand how Digital Twins facilitate safer and more effective virtual training for complex tasks.
Introduction: The manufacturing sector, a driving force behind Industry 4.0, is undergoing a profound transformation powered by Digital Twins. By creating dynamic virtual replicas of individual machines, production lines, operational processes, and even entire factories, manufacturers gain unprecedented capabilities to monitor, analyze, predict, and optimize their operations. This enables a crucial shift from reactive problem-solving (fixing things after they break) to proactive and predictive management, leading to significant improvements in efficiency, quality, safety, and resilience.
Case Study: Predictive Maintenance (PdM) - Beyond Scheduled Check-ups: This is one of the most mature and impactful applications, directly tackling the high costs associated with equipment failure and unplanned downtime. * Traditional vs. PdM: Think of traditional maintenance like this: Reactive is fixing your car after it breaks down on the highway. Preventive is changing the oil every 5,000 miles, regardless of whether it's needed (sometimes wasteful, sometimes insufficient). Predictive Maintenance (PdM), enabled by Digital Twins, is like having sensors in your car continuously analyzing engine performance, oil condition, and vibration patterns to tell you, "Based on current conditions and wear patterns, you'll likely need an oil change and potentially a bearing check within the next 800 miles to avoid a breakdown." It aims for maintenance at the optimal moment - just before failure occurs. * How it Works: Sensors on critical machinery (motors, pumps, bearings, robots, etc.) continuously stream operational data (vibration, temperature, pressure, power consumption, acoustic signatures, oil analysis results) to the machine's Digital Twin. * AI/ML Analysis: Machine learning algorithms analyze this stream of real-time and historical data, identifying subtle anomalies and complex patterns that often precede component degradation or outright failure. These algorithms need sufficient data (or sometimes physics-based models) to learn these failure signatures. * Benefits: The Digital Twin can forecast when a specific component is likely to fail and often why (identifying the probable failure mode). This allows maintenance to be scheduled precisely when needed, resulting in: * Minimized unplanned downtime (often the biggest cost). * Reduced maintenance costs (optimizing labor, replacing only necessary parts). * Prevention of catastrophic secondary damage (e.g., a failing bearing causing gearbox destruction). * Improved safety by addressing issues before they become hazardous. * Extended overall asset lifespan. * Example: A Digital Twin monitoring an industrial gearbox detects an unusual high-frequency vibration pattern combined with a slight, steady temperature increase. The AI analysis predicts a specific bearing failure with 85% confidence within the next 7-10 operational days. Maintenance is scheduled during a planned brief shutdown the following week, replacing only the identified bearing, thus avoiding potentially days of lost production from an unexpected, catastrophic gearbox seizure.
Process Simulation and Optimization: Digital Twins aren't limited to individual assets; they can represent entire processes or production lines, enabling holistic optimization. * Virtual Commissioning: Before building or modifying a physical production line, its Digital Twin (often connected to the actual control system software like PLCs) can simulate material flow, test control logic, validate robotic programming, identify potential bottlenecks, and optimize the layout virtually. This drastically reduces the time, cost, errors, and risks associated with on-site commissioning and startup. * Real-time Optimization: Once operational, the Digital Twin, fed with live data (machine status, buffer levels, energy use, quality readings), acts as a virtual sandbox. Managers can ask: "What happens if we increase the speed of conveyor belt X?" or "How does altering the parameters of machine Y affect overall throughput versus energy consumption?" They can test these scenarios risk-free on the twin to continuously fine-tune operating parameters based on current conditions and business goals (e.g., maximizing output during peak demand, minimizing energy use overnight). * Example: A beverage bottling plant uses a Digital Twin of its packaging line. By simulating different combinations of filler speeds, labeler settings, and accumulation table logic based on real-time product flow and downstream machine status, they identify an optimal configuration that increases Overall Equipment Effectiveness (OEE) by 8% without any new hardware investment.
Real-time Supply Chain Tracking and Management: Digital Twins can extend beyond the factory floor to model and manage logistics and entire supply chains, providing crucial end-to-end visibility and resilience. * Enhanced Visibility: Tracking the real-time location and condition (e.g., temperature, humidity, shock for sensitive goods like pharmaceuticals or fresh food) of shipments using IoT sensors on containers, pallets, or even individual packages, all linked to a Digital Twin of the supply network. * Resilience Planning & Response: Simulating the impact of potential disruptions (e.g., port delays, extreme weather, supplier outages, traffic jams) on the Digital Twin allows companies to proactively identify vulnerabilities, evaluate alternative routes or sourcing strategies, dynamically reallocate inventory, and improve overall supply chain responsiveness and planning.
Enhanced Quality Control: Digital Twins help improve product quality and accelerate issue resolution by creating a clear link between process parameters and quality outcomes. * Process-Quality Correlation: By correlating sensor data captured during production (e.g., injection molding pressure/temperature profiles, welding parameters, curing times) with subsequent quality inspection results for specific batches or serialized items, the Digital Twin can help pinpoint the precise operating conditions or material variations most likely to cause defects. This enables faster identification of root causes and potentially real-time process adjustments to prevent future defects. * Digital Thread & Faster Root Cause Analysis: When a defect does occur, the Digital Twin, as part of a broader 'digital thread' (a record connecting all data from design through manufacturing to service for a specific product instance), provides a rich, easily accessible historical dataset of the exact conditions, materials, and processes involved. This dramatically speeds up root cause analysis compared to manually sifting through disparate logs, spreadsheets, and paper records.
Virtual Training Environments: Complex manufacturing equipment and procedures often require extensive training, which can be costly and sometimes hazardous on live equipment. * Safe, Realistic, Immersive Learning: Using VR/AR interfaces connected to a machine's or process's Digital Twin, trainees can practice operating complex machinery, performing intricate maintenance procedures, or responding to simulated emergency scenarios (like equipment shutdowns or safety incidents). They do this in a safe, highly realistic virtual environment that accurately mirrors the real system's behavior and response, driven by the twin's data and models. * Benefits: Reduces risks associated with training on live, operational equipment; lowers training costs (travel, potential equipment damage or downtime); allows practice on rare but critical emergency events; can improve skill acquisition, retention, and consistency.
Key Concepts: * Predictive Maintenance (PdM): Using sensor data and analytical tools (often AI/ML) to detect anomalies and predict potential failures in equipment or processes, enabling optimized, proactive maintenance scheduling just before failure. * Virtual Commissioning: Testing and validating automation control logic, system behavior, and operational workflows using a simulation model (Digital Twin) connected to the real control system software, performed before physical installation and startup to de-risk the process. * Process Optimization: Continuously fine-tuning operational parameters within a system (like a production line) based on real-time data and simulation to achieve the best possible outcomes (e.g., maximizing throughput, minimizing energy use, reducing waste, improving quality). * Supply Chain Visibility: The ability to track products, materials, and assets in near real-time as they move through the supply network, including their condition. * Digital Thread: A data-driven architecture creating an accessible, integrated view of an asset's data throughout its entire lifecycle (design, production, operation, service), often leveraging Digital Twins as key components.
Knowledge Check: 1. How does a Digital Twin primarily enable Predictive Maintenance (PdM) compared to traditional time-based schedules? * a) By providing an interactive 3D model of the machine for technicians. * b) By analyzing real-time sensor data with AI/ML to detect early warning signs and forecast the optimal time for maintenance before a failure occurs. * c) By automatically ordering and stocking all possible spare parts in advance. * d) By allowing engineers to remotely control the machine's speed. (Correct Answer: b)
Summary: In manufacturing and operations, Digital Twins serve as powerful catalysts for Industry 4.0, driving significant improvements. They enable a paradigm shift from reactive to proactive maintenance through accurate prediction (PdM). They allow risk-free process simulation, virtual commissioning for faster startups, and continuous optimization based on live data. Furthermore, they enhance supply chain visibility and resilience, improve quality control through better process correlation and faster root cause analysis via the digital thread, and provide safe, effective virtual training environments. Collectively, these applications lead to increased efficiency, reduced costs, higher quality products, improved safety, and greater operational agility and competitiveness.
4. Transforming Design: From Products to Cities
Learning Objectives: * Understand how Digital Twins accelerate product development cycles through enhanced virtual testing and simulation. * Explain the role of Digital Twins in simulating product performance under diverse real-world conditions before physical prototyping. * Recognize how Digital Twins extend Building Information Modeling (BIM) for dynamic building lifecycle management. * Identify diverse applications of Digital Twins in urban planning, infrastructure management, and smart city initiatives. * Become aware of the potential, challenges, and ethical considerations of emerging uses in personalized healthcare.
Introduction: Beyond the factory floor, the power of the Digital Twin concept is fundamentally reshaping design processes across vastly different scales. From optimizing individual consumer products and complex engineered systems, to managing buildings and infrastructure networks, and even planning entire cities, Digital Twins offer a new paradigm. By enabling sophisticated virtual testing, simulation of complex real-world conditions, and incorporating feedback loops throughout an asset's lifecycle, they empower designers, engineers, architects, and planners to create more efficient, resilient, sustainable, and user-centric solutions faster and more cost-effectively.
Accelerating Product Development: Traditional product development often relies on lengthy and costly cycles of designing, building physical prototypes, testing them, identifying flaws, and iterating. Digital Twins dramatically streamline this. * Virtual Prototyping & Enhanced Testing: Digital Twins allow extensive testing and validation in a virtual environment before committing resources to expensive physical prototypes. Analogy: It's like running thousands of flight simulations for a new aircraft design in a virtual wind tunnel and under simulated extreme weather conditions before building the first physical wing section. Engineers can subject high-fidelity digital replicas of products (cars, engines, medical devices, electronics) to simulated: * Structural stresses and thermal loads. * Aerodynamic or fluid dynamic forces. * Electromagnetic interference. * Complex usage scenarios and edge cases. * Manufacturing process feasibility. * Rapid Iteration & Multi-Objective Optimization: Design changes can be made virtually and their impact assessed almost instantly within the Digital Twin. This allows for far more iterations and helps engineers balance competing objectives (e.g., performance vs. weight vs. cost vs. manufacturability) much more effectively than relying solely on physical testing. * Performance Simulation under Real-World Conditions: Simulating how a product will perform under a wide range of expected operating conditions (different climates, user behaviors, load profiles) early in the design phase helps identify potential weaknesses, validate that requirements are met, and optimize for robustness, efficiency, and user experience across its intended operational life. * Example: An automotive company uses a Digital Twin of a new electric vehicle battery system. They simulate charging/discharging cycles under extreme temperatures, model thermal runaway scenarios, test battery management system algorithms, and predict battery degradation over years of simulated use, refining the design for safety, range, and longevity long before building costly battery packs for physical testing.
Architecture, Engineering, Construction (AEC) and BIM Evolution: In the building and infrastructure sector, Digital Twins represent a powerful evolution from traditional Building Information Modeling (BIM). * From Static BIM to Living Digital Twin: BIM provides a rich, data-packed 3D model representing the 'as-designed' or 'as-built' state of a building or infrastructure asset, including its components, materials, and systems. Analogy: BIM is like a detailed architectural blueprint combined with a comprehensive inventory list. A Digital Twin takes this foundation and makes it live by connecting the model to real-time data streams from the occupied and operational asset. This data comes from IoT sensors monitoring temperature, occupancy levels, energy consumption, air quality, structural stress, equipment status (HVAC, elevators), security systems, etc. It bridges the crucial gap between the static design model and the dynamic 'as-operated' reality. * Dynamic Lifecycle Management: This creates a living digital replica used throughout the asset's entire lifecycle: validating design assumptions against actual performance, monitoring construction progress, optimizing operational efficiency (e.g., dynamically adjusting HVAC and lighting based on real-time occupancy data), streamlining facilities management (using predictive maintenance for elevators, HVAC, plumbing based on sensor data), and planning future renovations or retrofits more effectively based on actual usage patterns and building health. * Example: A Digital Twin of a large commercial office building integrates its BIM data with real-time sensor feeds for occupancy, lighting levels, temperature, and CO2. The building management system uses the twin's insights to automatically adjust lighting and ventilation zone-by-zone, optimizing occupant comfort while achieving significant energy savings compared to static schedules. Facility managers use it to monitor HVAC equipment health and schedule maintenance proactively.
Urban Planning and Smart Cities: Digital Twins are becoming indispensable tools for understanding, managing, and planning the immense complexity of modern urban environments. * Simulating Complex Urban Dynamics: Planners can create Digital Twins of city districts or entire cities, integrating diverse, dynamic datasets covering traffic flow (vehicles, cyclists, pedestrians), public transport usage, energy grid load and production, water distribution networks, air quality, noise pollution, waste management logistics, building energy usage, and even relevant socio-economic data. * Data-Driven Scenario Planning & Policy Testing: The true power lies in simulation. Planners can use the Digital Twin to rigorously model the potential impact of proposed interventions before making costly and potentially disruptive real-world investments. Examples include: * Simulating the effect of a new subway line or bike lanes on traffic congestion and air quality. * Assessing the impact of a large housing development on local infrastructure (schools, utilities, roads). * Testing different traffic signal timing strategies to reduce delays. * Evaluating the effectiveness of urban greening initiatives on reducing the heat island effect. * Modeling the deployment of renewable energy sources or EV charging infrastructure. This allows for evidence-based decision-making, better stakeholder engagement through visualization, and optimized urban development strategies. * Environmental Impact Analysis: Simulating the effects of different urban planning choices or climate change scenarios (e.g., increased rainfall, sea-level rise) on energy consumption, water resource management, greenhouse gas emissions, flood risk, and emergency response planning. * Example: A coastal city develops a Digital Twin integrating topographical data, building models, real-time weather data, river flow rates, and sea-level rise projections. They use it to simulate the potential extent and depth of flooding during major storm surges under various climate scenarios. This helps them identify the most vulnerable neighborhoods, test the effectiveness of proposed flood defenses (like sea walls or absorbent green infrastructure), optimize emergency evacuation routes, and allocate resources for resilience measures more effectively.
Infrastructure Management: Monitoring the health, performance, and safety of critical infrastructure (bridges, tunnels, dams, grids, pipelines) is vital for public safety and economic continuity. * Real-time Asset Monitoring & Health Assessment: Digital Twins of critical infrastructure integrate data from various sensors (strain gauges, vibration sensors, corrosion sensors, temperature sensors, acoustic sensors for leaks, GPS for displacement, flow meters) to monitor structural integrity, operational status, and environmental impacts in real-time. * Predictive Maintenance & Enhanced Resilience: Analyzing trends and anomalies in sensor data allows infrastructure operators to predict potential failures - identifying developing structural weaknesses in a bridge before they become critical, detecting small leaks in a water pipeline before they rupture, predicting overload conditions in a power grid substation. This enables targeted, preventative maintenance, enhances public safety, improves service reliability, extends the lifespan of aging assets, and optimizes maintenance budgets.
Emerging Applications: Personalized Healthcare: The Digital Twin concept is extending towards modeling the human body itself, promising a future of highly personalized medicine, though significant challenges remain. * Patient Digital Twins (Conceptual & Developmental): The vision involves creating a dynamic virtual replica of an individual patient. This twin would integrate data from their electronic health records (EHR), genomic information, real-time data from wearable sensors (heart rate, activity, glucose levels), medical imaging (MRI, CT scans), and potentially lifestyle factors (diet, sleep). * Potential Uses (Research & Future Clinical): * Simulating the potential effectiveness and side-effects of different drug treatments or surgical procedures on the individual patient's twin before administering them in reality. * Optimizing personalized treatment plans and dosing regimens. * Providing clinicians with deeper insights into individual disease progression or response to therapy. * Potentially serving as virtual test subjects for new drug development or clinical trial design. Digital Twins of specific organs (like the heart or brain based on medical imaging and simulation) are already being used in research settings to understand disease mechanisms and test interventions virtually. * Significant Challenges: Realizing the full vision of personalized patient twins requires overcoming immense hurdles related to: standardizing and integrating diverse health data sources, ensuring extremely high model fidelity and validation, managing computational costs, and critically, addressing profound data privacy, security, and ethical considerations regarding the use of sensitive personal health information.
Key Concepts: * Virtual Prototyping: Creating and testing digital models of products or systems extensively in a simulated environment to evaluate characteristics and performance before physical creation, reducing reliance on physical prototypes. * Building Information Modeling (BIM): A process for creating and managing digital representations of the physical and functional characteristics of buildings and infrastructure, primarily focused on design and construction documentation. * Urban Dynamics: The complex, ever-changing interplay of systems within a city, including transportation, energy, population movement, land use, social interactions, and the environment. * Infrastructure Asset Management: The systematic lifecycle process of planning, acquiring, operating, maintaining, upgrading, and disposing of physical infrastructure assets cost-effectively, reliably, and safely. * Personalized Medicine: Tailoring medical prevention strategies, diagnostic approaches, and therapeutic treatments to the individual genetic, environmental, and lifestyle characteristics of each patient.
Knowledge Check: 1. How does integrating real-time sensor data differentiate a Building Digital Twin from a static BIM model for lifecycle management? * a) The Digital Twin uses older software than BIM. * b) The Digital Twin connects the BIM model (or its evolution) to live data from the operating building, creating a dynamic representation of its actual performance and condition, enabling ongoing optimization and predictive maintenance beyond just design and construction. * c) Only BIM models contain information about building materials. * d) Digital Twins are used only for residential buildings, while BIM is for commercial. (Correct Answer: b)
Summary: Digital Twins are transforming design and planning across multiple domains by enabling powerful virtual simulation and analysis. They accelerate product development through comprehensive virtual prototyping and performance testing under diverse conditions. In the built environment, they evolve static BIM into living models that bridge the gap between design intent and actual operation, optimizing lifecycle management for buildings and infrastructure. For cities, Digital Twins offer unprecedented capabilities for simulating complex urban dynamics, testing policies risk-free, and planning more sustainable and resilient development. While still emerging and facing significant ethical and technical hurdles, applications in personalized healthcare based on virtual patient models represent a potentially revolutionary frontier, aiming to tailor treatments to individual biology and physiology.
5. Key Benefits and Strategic Advantages
Learning Objectives: * Identify the major operational and financial benefits derived from implementing Digital Twins. * Understand how Digital Twins facilitate faster, more informed, and data-driven decision-making across an organization. * Recognize the role of Digital Twins in accelerating innovation cycles and reducing time-to-market for new products and services. * Appreciate the significant positive impact of Digital Twins on risk management, operational safety, sustainability, and overall business resilience.
Introduction: Adopting Digital Twin technology is far more than just a technological upgrade; it represents a fundamental strategic shift capable of delivering significant, often quantifiable, competitive advantages across diverse industries. These benefits span improved operational efficiency, substantial cost reductions, accelerated innovation, enhanced decision quality, better risk management, and improved safety and sustainability. Collectively, these advantages provide a strong justification for investment and drive tangible business value for organizations that successfully implement and scale their Digital Twin initiatives.
1. Increased Operational Efficiency and Resource Optimization: By providing a real-time, holistic, and dynamic view of operations, Digital Twins empower organizations to continuously monitor performance, swiftly identify inefficiencies, and allocate resources more effectively. * Enhanced Process Visibility & Bottleneck Removal: Gaining clear, granular insight into complex processes (e.g., manufacturing lines, supply chains, building energy use, grid operations) allows for precise identification of bottlenecks, idle times, waste sources (energy, materials), and underutilized assets that might be hidden in aggregated data. * Optimized Resource Consumption: Leveraging real-time data and predictive models within the twin allows for optimizing the consumption of energy, raw materials, water, and other resources based on actual demand, operational conditions, and even external factors (like energy pricing or weather forecasts). This leads directly to cost savings and improved environmental sustainability. * Throughput Maximization & Performance Tuning: Utilizing simulations based on live operational data allows managers to test different operating parameters (machine speeds, process schedules, logic configurations) within the virtual environment to identify adjustments that maximize output, improve quality yield, or optimize other key performance indicators (KPIs) without disrupting physical operations. * Example: A logistics company employs a Digital Twin of its distribution network, integrating real-time vehicle GPS data, traffic conditions, weather forecasts, fuel levels, cargo information, and warehouse inventory status. This allows dispatchers to dynamically optimize delivery routes in real-time, proactively rerouting vehicles around congestion, reducing fuel consumption, improving on-time delivery percentages, and enabling warehouse managers to better anticipate arrival times and optimize staffing for loading/unloading.
2. Significant Reduction in Maintenance Costs and Unexpected Downtime: Predictive Maintenance (PdM), a flagship application enabled by Digital Twins, offers substantial financial and operational advantages over traditional maintenance approaches (reactive or purely time-based). * Minimized Unplanned Downtime: The ability to predict failures before they occur allows organizations to shift away from costly reactive maintenance ('fix-it-when-it-breaks') and drastically reduce unplanned interruptions to production, service delivery, or critical operations. This is often the single largest financial benefit. * Optimized Maintenance Scheduling & Costs: Performing maintenance interventions precisely when needed based on the actual condition and predicted failure risk of an asset, rather than on fixed time intervals, eliminates unnecessary maintenance tasks, reduces labor costs, minimizes spending on spare parts (only replacing what's needed, when needed), and optimizes the scheduling of maintenance crews and resources. * Extended Asset Lifespan & Improved Reliability: By catching potential issues early and preventing minor problems from escalating into catastrophic failures, and by operating assets within optimal parameters informed by the twin, organizations can often extend the useful operational life of expensive machinery, equipment, and infrastructure, improving overall system reliability and return on assets. * Example: An energy company utilizes Digital Twins for its fleet of offshore wind turbines. By analyzing vibration, temperature, and operational data, the twins predict potential component failures (like gearbox bearing wear or blade erosion) weeks in advance. This allows the company to schedule proactive maintenance during favorable weather windows, grouping tasks efficiently, optimizing vessel chartering and crew deployment, resulting in a reported 25% reduction in maintenance costs and a significant increase in turbine availability (thus reducing lost revenue).
3. Improved and Faster Decision-Making: Digital Twins equip decision-makers at all levels - from frontline operators to engineers to executives - with accurate, contextualized, real-time data and powerful predictive insights. This fundamentally shifts decision-making away from reliance on intuition, historical averages, gut feelings, or incomplete information. * Data-Driven Insights: Basing operational adjustments, design choices, investment decisions, and strategic planning on a clear, shared understanding of the current state and, crucially, the predicted future state of assets, processes, and systems. * Scenario Analysis & 'What-If' Simulation: Providing a powerful capability to quickly and cheaply evaluate the potential outcomes, trade-offs, and risks of different decisions or external events in the risk-free virtual environment before committing resources in the real world. Examples: "What is the predicted impact on production if our key supplier is shut down for a week?" "What is the energy saving potential if we upgrade these pumps?" "How would altering the traffic light phasing affect congestion during rush hour?" * Enhanced Cross-Functional Collaboration: Offering a common, data-rich, often visualized platform (acting as a 'single source of truth') that diverse teams (engineering, operations, maintenance, planning, finance) can use for shared understanding, collaborative problem-solving, and more aligned, evidence-based decision-making.
4. Enhanced Innovation Through Rapid Experimentation and Validation: The capability to model, simulate, and rigorously test new ideas virtually significantly accelerates the innovation cycle for products, processes, and services. * Faster Virtual Prototyping: Radically reducing the time and expense associated with designing, building, and testing multiple iterations of physical prototypes for new products or proposed process improvements. * Risk-Free Testing & Exploration: Allowing engineers and designers to experiment boldly with novel designs, materials, algorithms, operational strategies, or control logic using the Digital Twin, without any risk of disrupting live operations, damaging physical assets, or compromising safety. * Exploring a Wider Solution Space: Because the cost and time per virtual experiment are dramatically lower than physical testing, teams can explore a much wider range of possibilities and conduct more complex multi-variable optimizations. This increases the likelihood of discovering truly innovative, highly optimized, and robust solutions that might have been too costly or time-consuming to investigate using traditional methods. * Example: A pharmaceutical company develops a Digital Twin of its complex bioreactor process used for producing a new biologic drug. They use the twin to simulate the impact of hundreds of different combinations of critical process parameters (temperature profiles, nutrient feeding strategies, agitation speeds, pH levels) on final product yield and purity. This allows them to identify an optimized production recipe much faster and with significantly fewer costly and time-consuming laboratory experiments, accelerating the critical time-to-market for the new therapy.
5. Better Risk Assessment, Management, and Improved Safety Outcomes: Understanding potential failure modes, simulating hazardous scenarios, and providing operators with better context-aware information all contribute to more effective risk mitigation efforts and safer operating environments. * Proactive Risk Identification & Mitigation: Employing simulation and predictive analytics within the Digital Twin to identify potential failure points, safety hazards, compliance issues, or security vulnerabilities in complex systems before they manifest physically. Examples include predicting potential structural weaknesses in aging infrastructure under future load scenarios or identifying process deviations in a chemical plant that could lead to unsafe conditions. * Emergency Response Planning & Training: Using a high-fidelity Digital Twin of a facility (e.g., factory, power plant, hospital, city district) to simulate various emergency scenarios (equipment failure, fire, chemical spill, cyber-attack, natural disaster). This allows organizations to develop, test, and refine emergency response plans and procedures in a realistic virtual setting, identifying weaknesses and improving coordination. * Enhanced Situational Awareness & Safer Training: Providing operators with richer real-time context and predictive insights from the Digital Twin to improve their situational awareness during normal operations and stressful events. Furthermore, training personnel on hazardous tasks (e.g., complex maintenance, emergency shutdown procedures) in an immersive, safe virtual environment linked to the Digital Twin improves preparedness, critical decision-making under pressure, and reduces the likelihood of errors and accidents in the real world.
Key Concepts: * Operational Efficiency: Maximizing the output (products, services) achieved for a given set of resource inputs (time, energy, materials, cost), or minimizing the resources needed for a given output. * Condition-Based Maintenance (CBM) & Predictive Maintenance (PdM): Maintenance strategies triggered by the actual condition of an asset (CBM, based on sensor data) or a prediction of future failure (PdM, often using AI/ML on sensor data), rather than fixed schedules. * Scenario Analysis: The process of using a model (like a Digital Twin) to explore the potential consequences of different decisions, events, or future conditions ('what-if' analysis). * Innovation Cycle: The end-to-end process from generating a new idea through its development, testing, validation, refinement, and eventual implementation or market introduction. * Risk Management: The systematic process of identifying potential risks (threats or opportunities), assessing their likelihood and potential impact, prioritizing them, and implementing strategies to mitigate threats or capitalize on opportunities.
Knowledge Check: 1. Which strategic advantage is most directly related to using Digital Twins for 'what-if' analysis and simulating process changes before physical implementation? * a) Extending asset lifespan. * b) Improved and faster decision-making by evaluating options and their consequences virtually, thus reducing implementation risks. * c) Enhanced cross-functional collaboration. * d) Reduced unplanned downtime. (Correct Answer: b)
Summary: The strategic advantages offered by Digital Twins are compelling and wide-ranging. They drive significant improvements in operational efficiency and resource optimization by providing deep visibility and enabling data-driven tuning. They drastically reduce maintenance costs and unplanned downtime through powerful predictive maintenance capabilities. They enable faster, more informed, and data-driven decision-making by leveraging real-time data and risk-free 'what-if' simulation. They accelerate innovation by facilitating rapid virtual experimentation and validation. Finally, they enhance risk management and improve safety through proactive hazard identification, better emergency preparedness, and safer training methods. These benefits collectively contribute to improved profitability, increased resilience, greater sustainability, enhanced safety, and a stronger competitive position in the marketplace.
6. Challenges, Ethics, and Limitations
Learning Objectives: * Recognize the significant investment, technical complexity, and integration challenges associated with implementing Digital Twins. * Understand critical data-related concerns: cybersecurity threats, data privacy implications, accuracy and fidelity requirements, and ownership ambiguities. * Appreciate the need for specialized multidisciplinary skills and potential organizational changes for successful adoption. * Identify key ethical considerations and potential negative societal impacts surrounding the widespread use of Digital Twin technology that require careful consideration.
Introduction: Despite the immense potential and numerous benefits, the journey to successfully implementing, scaling, and deriving sustained value from Digital Twin technology is often paved with significant obstacles. Organizations face substantial technical, financial, and organizational hurdles. Furthermore, the increasing power and pervasiveness of Digital Twins raise critical ethical questions regarding data usage, potential bias, surveillance implications, and accountability that must be proactively addressed for responsible and trustworthy adoption.
1. High Initial Investment and Integration Costs: Developing and deploying a sophisticated Digital Twin capable of delivering significant value often requires substantial upfront investment across multiple fronts. * Hardware Costs: Purchasing, installing, and maintaining potentially large numbers of diverse IoT sensors, actuators, edge computing devices, and potentially upgrading network infrastructure (wired or wireless) to handle the data load. * Software & Platform Costs: Licensing fees or ongoing subscription costs for specialized Digital Twin platforms (often cloud-based), modeling and simulation software, AI/ML development tools, data management systems, and advanced visualization solutions. * Expertise & Personnel Costs: Hiring or training specialized personnel skilled in diverse areas like IoT engineering, data science, AI/ML, cloud architecture, cybersecurity, domain-specific modeling (e.g., physics, manufacturing processes, urban systems), data integration, and user interface design. * Integration Effort & Complexity: This is often underestimated. Significant time, effort, and specialized skills are required to integrate the various components of the Digital Twin technology stack with each other and, crucially, with existing, often siloed, enterprise IT systems (like ERP, MES, PLM, asset management) and operational technology (OT) systems (like SCADA, PLCs). Analogy: Integrating Digital Twins can be like trying to connect modern smart home devices seamlessly with the original plumbing and electrical systems of a century-old house - it requires careful planning, specialized adapters, and significant effort. * ROI Justification: Clearly demonstrating a compelling Return on Investment (ROI) to justify the significant upfront costs can be challenging, especially for complex, large-scale implementations where benefits might be indirect or accrue over time. Well-defined pilot projects are often crucial to prove value and secure buy-in for broader deployment.
2. Complexity of Integration with Legacy Systems: Most organizations operate within existing ecosystems of operational technology (OT) and information technology (IT) systems, many of which were not designed for the kind of open connectivity and data sharing required by Digital Twins. * Interoperability Barriers: Older machinery or legacy control systems may lack modern communication interfaces, use proprietary (closed) protocols, or simply not generate the needed data, making data extraction difficult, costly, or sometimes impossible without significant retrofitting or replacement. * Data Silos & Heterogeneity: Essential data for the Digital Twin often resides in disparate systems (process historians, maintenance databases, quality spreadsheets, CAD files, ERP records) with different owners, inconsistent formats, varying levels of quality, and lack of common identifiers, making data aggregation, harmonization, and contextualization a major hurdle. * OT/IT Convergence Challenges: Bridging the gap between the operational technology (OT) world (traditionally focused on real-time control, reliability, and physical safety, often with older systems) and the information technology (IT) world (focused on data processing, enterprise applications, and cybersecurity, often with faster refresh cycles) requires careful architectural planning, robust security measures that respect both domains, and often significant organizational and cultural alignment between these historically separate teams.
3. Data Security, Privacy, and Ownership Concerns: Digital Twins thrive on vast streams of data, often highly sensitive, creating significant security and privacy risks that must be rigorously managed. * Expanded Attack Surface & Cybersecurity Threats: The proliferation of connected sensors, edge devices, cloud platforms, network connections, and APIs significantly increases the potential entry points for cyber-attacks. Protecting the entire Digital Twin ecosystem (data in transit, data at rest, algorithms, models, control interfaces) is paramount. Threats include data breaches (theft of sensitive operational or design data), denial-of-service attacks (disrupting operations), and malicious manipulation (e.g., data poisoning - feeding false data to mislead AI models and cause incorrect predictions or harmful actions). These risks are amplified when twins can influence or control physical systems. * Data Privacy Risks: When Digital Twins involve data related to people - such as smart buildings tracking occupant movements or energy usage, wearable sensor data in potential healthcare twins, or worker location/performance monitoring via connected tools - strict adherence to privacy regulations (like GDPR, CCPA, HIPAA) is non-negotiable. Ensuring data anonymization where appropriate, obtaining informed consent, implementing robust access controls, and maintaining ethical data handling practices are critical to avoid violations and maintain trust. * Data Ownership and Governance Ambiguities: As data flows between asset owners, equipment manufacturers, technology platform vendors, and end-users, establishing clear policies and contractual agreements on who owns the raw sensor data, the processed insights, the derived AI models, and the twin itself can be complex. Defining how this data can be used, shared, monetized, and secured, especially in multi-party collaborations (like supply chains or smart city ecosystems), requires careful consideration and clear governance frameworks.
4. Ensuring Data Accuracy, Model Fidelity, and Timeliness: The effectiveness of a Digital Twin hinges entirely on the quality of its inputs: the data it receives and the accuracy of its underlying models. The principle of 'Garbage In, Garbage Out' is acutely relevant. * Data Quality, Cleansing, and Trustworthiness: Inaccurate, incomplete, noisy, biased, or untimely sensor data will inevitably lead to flawed analysis, incorrect predictions, poor decisions, and potentially unsafe outcomes. Robust processes for sensor calibration, data validation, outlier detection, handling missing data, and data cleansing are vital but often resource-intensive. * Model Fidelity and Validation: The virtual model must accurately represent the relevant physical characteristics, behaviors, and underlying physics of its real-world counterpart to the degree required for the intended application. Building high-fidelity models requires deep domain expertise combined with data science skills. Furthermore, these models need ongoing validation and calibration against real-world data to ensure they don't drift or become inaccurate over time as the physical asset changes or degrades. * Synchronization and Latency: Maintaining near real-time synchronization between the state of the physical asset and its digital representation can be challenging due to network latency, data processing delays, or sensors reporting at different frequencies. For applications requiring fast control loops or immediate responses based on the twin's state, minimizing latency is critical.
5. The Need for Skilled Personnel and Organizational Change: Successfully developing, deploying, operating, and extracting sustained value from Digital Twins requires a workforce with a sophisticated blend of specialized and often scarce skills, along with organizational adaptation. * Multidisciplinary Skill Sets: Effective Digital Twin initiatives demand close collaboration between domain experts (e.g., mechanical engineers, chemical engineers, urban planners, clinicians who understand the physical asset/process), data scientists, AI/ML engineers, software developers, IoT specialists, cloud architects, cybersecurity experts, and user experience designers. * Talent Gap: There is often a significant shortage of personnel possessing the necessary cross-disciplinary expertise required to effectively bridge the physical and digital domains and manage the complexity of the technology stack. * Upskilling and Reskilling Imperatives: Organizations need to invest significantly in training and upskilling their existing workforce to work with these new technologies and data-driven approaches, or compete aggressively for scarce external talent. * Organizational Adaptation and Change Management: Implementing Digital Twins is not just a technology project; it often requires fundamental changes to existing workflows, roles, responsibilities, decision-making processes, and performance metrics. Fostering a data-driven culture and managing the associated organizational change is crucial for successful adoption and value realization.
6. Ethical Considerations and Societal Impact: As Digital Twins become more capable and potentially pervasive, they raise significant ethical questions and potential societal impacts that demand careful consideration and proactive governance. * Surveillance, Privacy, and Control: The ability to monitor assets, processes, environments, and potentially people in unprecedented detail raises concerns about excessive worker surveillance, the erosion of individual privacy in smart cities or connected homes, and the potential for misuse of this detailed information for manipulation or undue control. * Algorithmic Bias and Fairness: AI algorithms used within Digital Twins can inherit and amplify biases present in the historical data used to train them. This can lead to unfair or discriminatory outcomes. Examples: predictive maintenance schedules that disproportionately affect certain worker groups; resource allocation recommendations from urban planning twins that disadvantage specific neighborhoods; diagnostic predictions from healthcare twins that are less accurate for certain demographic groups. * Job Displacement and Workforce Transition: Automation and optimization driven by Digital Twins may automate tasks previously performed by humans, potentially leading to job displacement or significant changes in required skills for roles in areas like maintenance, operations, monitoring, and analysis. This necessitates proactive societal and organizational strategies for workforce transition, retraining, and addressing the socio-economic impacts. * Accountability and Liability: If a decision or action based on a Digital Twin's analysis or recommendation leads to failure, damage, injury, or other harm, determining accountability can become incredibly complex. Who is responsible? The developers of the AI algorithm? The providers of the potentially flawed data? The owners or operators of the asset who trusted the twin's output? The manufacturer of the sensor? The twin itself, if operating autonomously? Establishing clear lines of responsibility and liability frameworks is essential, especially for critical applications. * Transparency and Explainability (XAI): For Digital Twins to be trusted, especially in high-stakes situations or when driving autonomous actions, their reasoning needs to be understandable. Ensuring that the predictions or recommendations generated by the twin (particularly those driven by complex AI models) can be explained (Explainable AI - XAI) is crucial for debugging, validation, building user trust, ensuring fairness, and enabling meaningful human oversight.
Key Concepts: * Return on Investment (ROI): A performance measure used to evaluate the financial efficiency and profitability of an investment relative to its cost. * Legacy Systems: Older methods, technologies, computer systems (hardware or software), or application programs related to an outdated but often still functional system, which can pose integration challenges. * Interoperability: The ability of different information systems, devices, applications, or models to connect, access, exchange, integrate, and cooperatively use data in a coordinated manner. * Data Governance: The overall management of data assets in an organization, encompassing policies, standards, processes, and controls related to data quality, security, privacy, usability, and compliance. * Algorithmic Bias: Systematic and repeatable errors in a computer system (like an AI model) that create unfair outcomes, such as privileging or disadvantaging one arbitrary group over others based on learned patterns in biased data. * Explainable AI (XAI): Methods and techniques in artificial intelligence that allow human experts to understand the results or outputs created by AI models, providing transparency into the decision-making process.
Knowledge Check: 1. Which of the following represents a major challenge related to data quality for Digital Twins? * a) The high cost of cloud storage for large datasets. * b) The difficulty in creating visually appealing 3D models. * c) Ensuring that the sensor data feeding the twin is accurate, complete, timely, and trustworthy, because poor quality input data inevitably leads to flawed insights and unreliable predictions ('Garbage In, Garbage Out'). * d) The lack of available AI algorithms for analysis. (Correct Answer: c)
Summary: While transformative, Digital Twin adoption faces substantial hurdles that must be addressed. These include significant initial investment costs and complex integration efforts, particularly when dealing with legacy OT and IT systems. Critical concerns revolve around robust cybersecurity for an expanded attack surface (including novel threats like data poisoning), ensuring data privacy especially with personal data, maintaining high levels of data accuracy and model fidelity ('Garbage In, Garbage Out'), and navigating ambiguities in data ownership and governance. A significant skills gap exists, demanding investment in multidisciplinary talent and organizational adaptation to new data-driven workflows. Furthermore, profound ethical considerations regarding surveillance, algorithmic bias, potential job displacement, complex accountability issues, and the crucial need for transparency and explainability (XAI) must be carefully navigated to ensure the responsible, fair, and beneficial deployment of this powerful technology.
7. The Future Horizon: Evolution of Mirror Worlds
Learning Objectives: * Explore the anticipated deeper integration of Digital Twins with Extended Reality (AR/VR/MR) and their foundational role in the Metaverse concept. * Understand the critical importance of standardization for enabling interoperability, scalability, and interconnected Digital Twin ecosystems. * Consider the potential evolution towards more autonomous Digital Twins capable of self-optimization and self-healing. * Recognize trends likely to increase the accessibility and democratization of Digital Twin technology beyond large enterprises. * Reflect on the potential long-term societal impacts and the convergence towards the broader, interconnected vision of Mirror Worlds.
Introduction: The journey of Digital Twins is far from over; we are arguably still in the early stages of realizing their full transformative potential. Future developments promise deeper, more seamless integration with immersive technologies, greater levels of embedded intelligence and autonomy, increased accessibility for a wider range of users and organizations, and a gradual convergence towards the comprehensive, interconnected vision of Mirror Worlds. Understanding these future trajectories is key for long-term strategic planning, anticipating the next wave of innovation, and navigating the associated opportunities and challenges.
1. Deeper Integration with AR/VR/MR (Extended Reality - XR): The synergy between Digital Twins and immersive XR technologies, while emerging today, will become much tighter, more intuitive, and widespread, fundamentally changing how humans interact with digital information anchored to the physical world. * Seamless Contextual AR Overlays: Imagine a field technician wearing AR glasses looking at a complex machine. They could see real-time data streams (temperature, pressure), diagnostic insights ("vibration anomaly detected in bearing housing"), predictive alerts ("estimated time to failure: 72 hours"), and step-by-step holographic instructions for a repair procedure - all generated by the machine's Digital Twin and overlaid directly onto their view of the physical equipment. * Immersive VR Collaboration & Simulation: Globally distributed design teams, urban planners, or factory managers could convene inside a shared, persistent VR environment representing a complex Digital Twin (e.g., a proposed factory layout, a city district model under a simulated flood event, a new aircraft design undergoing virtual stress tests). They could collaboratively review designs, run interactive simulations, identify potential clashes or issues, and make decisions within a highly intuitive, shared spatial context, regardless of physical location. * More Natural Interaction: XR interfaces utilizing gestures, voice commands, eye-tracking, and haptics will provide more natural and efficient ways to interact with, manipulate, query, and understand the complex, multi-dimensional data contained within Digital Twins, moving beyond the limitations of traditional 2D screens, keyboards, and mice.
2. Foundational Role in the Development of the Metaverse: Digital Twins are increasingly recognized as essential infrastructure - the 'plumbing' or 'digital foundation' - needed to build persistent, economically viable, and physically grounded virtual environments, often conceptualized under the umbrella term 'Metaverse'. * Real-World Anchoring & Fidelity: Digital Twins provide the crucial, dynamic link between potential Metaverse experiences and physical reality. They ensure that virtual representations of objects, assets, processes, and environments within the Metaverse accurately reflect their real-world counterparts' current status, behavior, and physics, preventing the Metaverse from becoming entirely detached from reality. * Engine for Metaverse Economy & Experiences: Activities within the Metaverse could be directly powered by real-world Digital Twins. Examples: offering virtual test drives based on a car's high-fidelity Digital Twin that accurately simulates its performance; enabling remote operation or monitoring of physical factories via their twins accessed through a virtual control room; creating realistic virtual tourism experiences based on constantly updated city Digital Twins; facilitating virtual design reviews of products whose twins can be tested against simulated physics. * Ensuring Consistency & Interoperability: Achieving seamless transitions and data consistency between physical reality and its varied representations within different Metaverse platforms will heavily rely on robust, standardized Digital Twin architectures and interfaces.
3. Maturation of Industry Standards for Interoperability: Currently, the Digital Twin landscape is often fragmented, with different vendors' solutions using proprietary data formats, APIs, and modeling languages. This significantly hinders integration, scalability, and the ability to connect twins across organizational boundaries. * Critical Need for Standardization: As Digital Twin implementations scale and need to connect across complex ecosystems (e.g., linking component twins to machine twins to factory twins to supply chain twins; integrating city infrastructure twins from different departments), industry-wide standards become absolutely essential. Analogy: Think of the standardization of shipping containers - before standards, global trade was vastly more complex and expensive. Similarly, standardized Digital Twin protocols are needed for seamless data exchange and collaboration. * Key Areas for Standardization: This includes standardizing data formats and semantic models (ontologies) so twins can understand each other's data, common APIs for interaction, standardized communication protocols (building on existing ones like MQTT, OPC-UA), security frameworks, and model definition languages (like DTDL or contributions from ISO/IEC). * Consortia and Open Efforts: Organizations like the Digital Twin Consortium, W3C, buildingSMART, and various industry-specific bodies (e.g., in manufacturing, energy) are actively working to establish these crucial standards. * Benefits of Standardization: Widespread adoption will simplify integration, reduce vendor lock-in, enable the creation of powerful 'federated' or 'composite' Digital Twins (combining multiple twins), facilitate secure data sharing across ecosystems, and ultimately accelerate innovation and adoption.
4. Potential for Increasingly Autonomous Digital Twins: Future Digital Twins are expected to evolve beyond being primarily decision-support tools for humans. They will likely incorporate greater levels of autonomous control and self-optimization capabilities, driven by advancements in AI, particularly reinforcement learning. * Self-Optimizing & Self-Healing Systems: Imagine a Digital Twin monitoring a chemical process. Detecting an inefficiency or predicting an impending equipment issue, it could autonomously adjust operating parameters (temperature, flow rates) of the physical process to mitigate the risk, optimize performance based on changing goals (e.g., dynamically shifting between minimizing energy cost and maximizing throughput based on market demand), or even automatically trigger maintenance work orders or logistical requests. * AI-Driven Continuous Learning & Adaptation: AI-powered Digital Twins could continuously run simulations based on live data, learn from the outcomes of past actions, and adapt their underlying models and control strategies over time. This would enable them to autonomously optimize highly complex systems for multiple, potentially conflicting, objectives (e.g., efficiency, resilience, sustainability, quality) without requiring constant human intervention for every minor adjustment. * Ethical Oversight, Control & Explainability (XAI) are Crucial: This trend towards autonomy raises significant questions and concerns about control, reliability, security (guarding against unintended consequences or malicious manipulation of autonomous systems), and accountability (who is responsible if an autonomous twin makes a mistake?). Robust safety protocols, clear human oversight mechanisms ('human-in-the-loop' or 'human-on-the-loop'), and the parallel development of Explainable AI (XAI) techniques - allowing us to understand why an autonomous twin is making certain decisions - will be absolutely paramount for safe and trustworthy deployment.
5. Increased Accessibility and Democratization: While sophisticated, custom-built Digital Twins are currently often the domain of large enterprises due to cost and complexity, several trends point towards broader accessibility in the future. * Maturing Cloud Platforms & 'DTaaS': Major cloud providers are offering increasingly sophisticated, yet more standardized and easier-to-configure, Digital Twin platforms and services ('Digital Twin as a Service'). This lowers the barrier to entry by reducing the need for extensive infrastructure investment and specialized setup. * Low-Code/No-Code Development Tools: The emergence of more user-friendly development tools and templates requiring less specialized programming or data science expertise will enable domain experts to implement and manage basic Digital Twin functionalities for common use cases more easily. * Pre-built Models & Marketplaces: A growing ecosystem and potential marketplaces offering libraries of pre-built, validated Digital Twin models for common types of industrial equipment, building systems, or even standardized business processes could significantly accelerate deployment. * Focus on Small and Medium-sized Businesses (SMBs): As the technology matures and costs decrease, technology vendors are likely to tailor offerings specifically for the needs and budgets of SMBs, unlocking the benefits for a much larger segment of the economy.
6. Long-Term Societal Impacts and the Mirror World Vision: Looking further ahead, the proliferation and interconnection of increasingly sophisticated Digital Twins across all facets of life and industry begin to approach the original, comprehensive 'Mirror World' concept envisioned by Gelernter. This potential future carries profound societal implications. * Hyper-Personalization: From consumer products that dynamically adapt their behavior based on individual usage twins, to highly personalized medical treatments simulated on patient twins, to dynamically tailored urban services and real-time traffic management based on city-scale twins. * System-of-Systems Optimization: The ability to model, simulate, and optimize extremely complex, interconnected systems at unprecedented scales by linking vast networks of federated Digital Twins. Examples: optimizing global logistics networks in real-time, managing national energy grids integrating fluctuating renewables and electric vehicle charging demands, developing regional climate adaptation strategies based on integrated environmental and infrastructure twins. * Fundamental Societal & Ethical Questions: This potential future forces us to grapple with profound questions: the blurring lines between reality and simulation; the ethics of pervasive monitoring and predictive modeling of systems, environments, and potentially human behavior; the risk of exacerbating the digital divide (inequitable access to technology, data, and skills); defining data rights and individual agency in a mirrored world; and understanding the overall impact on human experience, autonomy, decision-making, and societal structures. * The Evolving Vision: The future likely involves a dynamic, data-rich, interactive digital layer increasingly mirroring and interacting with the physical world. This offers immense potential for understanding, efficiency, prediction, and control, but realizing this potential responsibly demands ongoing societal dialogue, robust ethical governance frameworks, and a steadfast commitment to human-centric innovation.
Key Concepts: * Extended Reality (XR): An umbrella term for technologies that blend the physical and digital worlds, including Augmented Reality (AR - overlays digital info onto the real world), Virtual Reality (VR - fully immersive digital environment), and Mixed Reality (MR - interactive digital objects integrated with the real world). * Metaverse: A term often used to describe future persistent, shared, 3D virtual spaces linked into a perceived virtual universe, envisioned as an evolution of the internet where digital and physical realities converge. * Interoperability: The ability of different systems, organizations, or components (like Digital Twins from different vendors) to exchange data and information meaningfully and use it effectively. * Autonomous Systems: Systems capable of operating, making decisions, and adapting to changing conditions over time without direct, continuous human intervention. * Digital Divide: The gap between demographics and regions that have access to modern information and communications technology (including the skills to use it) and those with limited or no access. * Explainable AI (XAI): Artificial intelligence models and techniques designed so that their operations and outputs can be understood by human experts, providing transparency and enabling trust.
Knowledge Check: 1. Why is the development of industry standards considered crucial for the future scaling and widespread adoption of Digital Twins? * a) Standards make Digital Twin software significantly more expensive to develop. * b) Standards limit innovation by restricting technological choices. * c) Standards enable different Digital Twin systems and platforms from various vendors and organizations to communicate, exchange data meaningfully, and work together seamlessly (achieving interoperability), which is essential for building complex, interconnected solutions (like supply chain or smart city twins) and avoiding vendor lock-in. * d) Standards eliminate the need for cybersecurity measures in Digital Twins. (Correct Answer: c)
Summary: The future trajectory of Digital Twins points towards deeper, more intuitive integration with immersive XR technologies, providing powerful new ways to visualize and interact with data in context, and playing a foundational role in enabling physically grounded Metaverse experiences. Achieving broad scalability and creating interconnected ecosystems hinges critically on the development and adoption of robust industry standards for interoperability. We can anticipate advancements towards more autonomous, self-optimizing twins capable of independent action, which simultaneously demands parallel progress in ethical governance, safety protocols, and explainability (XAI). Concurrently, trends towards cloud-based platforms ('DTaaS') and simplified tools promise increased accessibility, democratizing the technology beyond large corporations. Ultimately, these developments continue to push towards the larger, more integrated vision of Mirror Worlds, offering transformative potential for understanding and optimizing complex systems across society, while demanding ongoing dialogue and proactive governance to address the profound associated ethical, societal, and human implications.
Further Reading
- Digital Twin Consortium - Industry Resources & Glossary
- Gartner Research: Top Strategic Technology Trends (search within site for Digital Twin)
- Deloitte Insights: Digital Twin Reports (search within site)
- IBM: What is a Digital Twin? Overview
- Microsoft Azure Digital Twins Documentation
- AWS IoT TwinMaker Documentation
- ISO/IEC JWG 21 - Standards work on Digital Twin